PRINTING ON FABRIC |
 |
Reproducing digital images on fabric (also called "textiles") has many applications in both private and commercial realms. Printed fabrics may be used in sewing projects to produce unique items, displayed as banners or flags to promote businesses or events, or applied to the wall with an adhesive for a modern wallpaper option.
But in addition to the many uses, there are also many production methods for fabric printing, from manual to digital. Below is a summary of these methods, followed by an in-depth breakdown of each process.
|
SUMMARY
METHOD |
PROCESS |
COMMON USES |
Digital Printing |
A flatbed or roll-based printer is used to reproduce an image from a digital file on a fabric surface. |
Large scale and single copy, clothing logos, business advertising. |
Screen Printing |
A mesh screen is laid over the fabric and ink is drawn across its surface. The ink passes through unblocked holes in the shape of the image, transferring the ink to the fabric. |
T-shirts, large runs of the same image, non-fabric materials. |
Stencilling |
An image cut out of a rigid material is laid over the fabric and paint or ink is applied to the cut out sections. Places where the stencil blocks the fabric will remain the original color. |
Small scale projects, usually with a repetitive, tiled pattern. |
Block Printing |
Paint or dye is applied to a relief image carved or cut out of a block of wood, stone, or other substance. This stamp is then pressed to the fabric to transfer the ink in the shape of the image. |
Traditional fabrics, small batches of handmade items, repetitive patterns. |
Resist Dyeing |
Wax, mud, or a chemical agent that blocks dye reception is applied to sections of fabric. After dyeing, these sections are washed clean to reveal the original color of the fabric. |
Tie dye and batik prints, traditional tapestries and textiles. |
|
DIGITAL PRINTING
|
 |
PROCESS
Digital printing remains less common than more traditional methods of printing fabrics, but the possibilities and quality of the process has vastly improved in recent years. Once a digital design has been created, either from a photograph or scan of an original image, or rendered completely on the computer, there are various ways it can be digitally transferred to fabric.
In the case of a single image, a flatbed printer can be used to print precisely where the image needs to be. This is used for printing on pre-shaped fabrics, such as clothing or pillow cases. Depending on the ink, the fabric may need to be treated beforehand with an ink-receptive coating. Dye sublimation is another digital option for single images. An image is infused into polyester material using a printed image on transfer paper, and a heat press.
For large scale fabric printing, such as multiple yards of a repeated pattern for sale, a flatbed or roll-based inkjet printer may be used to imprint synthetic or natural fiber textiles (cotton, polyester, silk, nylon) with a tiled image. This is how most rolls of quilting fabric available at fabric stores was created. Smaller, full coverage images such as banners and flags for business advertising are often created using this method, as well.
A newer option that allows anyone with an inkjet printer to print on fabric is paper-backed fabric sheets. The paper makes the fabric rigid enough to pass through an ordinary printer, and can then be peeled off and discarded. Cotton, bamboo, and silk fabric papers are currently available.
At KeenART Media, we can reproduce any print on an adhesive fabric that can be affixed to indoor and outdoor surfaces and is water- and wrinkle resistant, wind tested, and reusable.
COMMON USES
- Large scale production of textiles for resale (quilting)
- Logos and designs on clothing
- Business signage and advertising
PROS
- Less waste than traditional methods - no transfer papers, only as much ink used as required (excess ink is stored).
- High print speeds result in high profit margins.
- Easier to customize than some traditional methods.
- Better for small print runs, due to shorter setup/preparation time.
CONS
- The printable width of the fabric will depend on the printer, but is usually limited to 60".
- Color fastness is uncertain in fabrics that must be washed repeatedly.
- No white ink, so areas of white will instead be the color of the fabric.
- Inks may be more expensive than dyes/inks used in other methods.
|

|
SCREEN PRINTING
|
 |
PROCESS
When screen printing, a stencil is created on a mesh frame. This may be done by coating the mesh in an emulsion, and then burning away some of this emulsion in the mirrored shape of the desired image. The emulsion will block the inks from reaching the fabric everywhere except where it has been removed. A different screen (frame) is used for each color, with different parts of the emulsion removed in each one.
Once the mesh frame is completed, it is laid over the fabric (with space between the mesh and the fabric) and the ink is place on top. A rubber squeegee moves the ink across the screen. Where the unblocked mesh is (the image), the ink will reach the fabric. Everywhere else, it will remain on top of the screen. This screen can be reused over and over for multiple pieces of fabric.
Depending on the desired outcome, the layers of ink may be left to dry between colors, or a wet-on-wet approach may be taken to achieve some blending.
COMMON USES
- T-shirts,
- Beyond fabric, used for printing on vinyl or plastics (decals, balloons, electronics).
- Thick film technology
PROS
- Techniques such as foil, flocking, or glitter can be used.
- Many finishes of ink or additives, such as gloss, puff, metallic, suede.
- The result is professional and high quality.
- Lasts through wash cycles.
CONS
- A lot of set up and preparation is required.
- Not practical for small quantities.
- High resolution/photographic images do not work well.
|

|
STENCIlLING
|
 |
PROCESS
Largely used for small runs of only one or a few items, stencilling involves applying paint onto fabric through a plastic, paper or vinyl pattern out of which an inverted image is cut - the cut out portions will appear on the fabric. Some stencils have a light adhesive backing that holds the stencil in place while it is painted over, and allows for easy removal and repositioning. Once the base image is painted, more detailed stencils may be laid over top and painted in different colors.
Color, in the form of inks, dyes, or paints, is painted or drawn into the cut out sections of the stencil. Usually, a small stencil is used as a repeated pattern across a length of fabric. Though this process is usually done by hand, stenciling machines do exist that pass portions of fabric beneath a metal stencil, applying a coat of ink or paint over the stencil at each pass. These machines were intended for single-color patters only.
Depending on the type of ink or dye used, a stenciled image may hold up well to wear and UV exposure, and retain its color through multiple washes.
COMMON USES
- Children's crafts
- T-shirts
- Small upholstery projects
PROS
- Used for various materials, including plastics and paper.
- Gives items a handmade, personal touch.
- Stencils themselves can be inexpensive or made at home.
CONS
- In order for the stencil to remain as one piece, thin ties must connect any cut out portions.
- Impractical for large orders.
- Some bleeding beneath the edge of the stencil is common
|
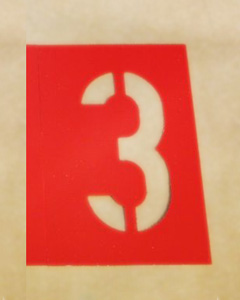
|
BLOCK PRINTING
|
 |
PROCESS
Basically the reverse process of stencilling, block printing requires the image to be cut or carved into a block of wood, stone, metal, rubber or plastic stamp. Paint, ink, or dye is applied to the face of the stamp block, which is then laid on the fabric and pressed or struck with a mallet, to evenly transfer the paint from the block.
Block printing is the earliest known type of fabric printing, and is still used in many countries and for handmade individual projects. Once the image has been transferred to the fabric, the block can be re-inked and used again and again. Extremely detailed images are possible and depend on the skill of the designer. Single-color images are most common, but different colors can be applied to different parts of the block, or additional colors can be added to the single-color print afterwards.
A block printing machine called the Perrotine was invented in 1834 that could cover larger areas at faster speeds. It is still used in some factories, primarily in Europe.
COMMON USES
- Hand-printing wraps and shawls in certain countries.
- T-shirts or small patters on other clothing fabrics.
- Small scale upholstery projects.
PROS
- Can be used for very simple or very intricate designs.
- If dyes are used, color fastness is achievable.
- It is a traditional, ancient method still applicable today.
CONS
- Extremely time consuming.
- Paint application to both the block and the fabric must be even and regular.
- Heavy textures may not print well because paint cannot reach dips in the fabric.
|
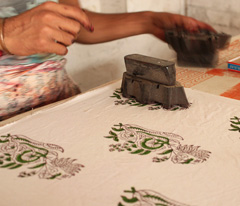
|
RESIST DYEING
|
 |
PROCESS
Resist dyeing (or Resist Printing) is a method by which a pattern is achieved on fabric by applying a coating that resists dye to certain sections of the cloth. When the dye is applied to the entire piece of material, those sections remain the original color while the untreated sections become the new color.
The most common coatings are wax, starch, or mud, which stick to the fabric during the dyeing process, and is washed or melted off once the dye is dry. A chemical agent may also be applied in more modern practices of this method. Alternately, sections that are not to be dyed may be clamped, tied off, or stitched over during the dyeing process and removed after. Once the fabric is dry, some resistant coatings can be reapplied to dye other sections.
COMMON USES
- Tie-dying
- Batik fabric prints
- Shawls, tapestries, and clothing
PROS
- The fabric is infused with the colors, instead of the inks sitting on top.
- Produces unique results on every piece.
- Set up and preparation can be simple.
- Materials are generally inexpensive.
CONS
- Impractical for large scale production.
- Identical reproductions are extremely difficult to achieve.
- Dyes can be messy and damage other clothing, tools, etc.
|
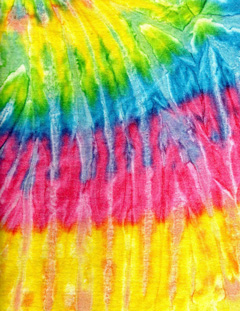
|
OTHER PRINTING METHODS
|
 |
BURN-OUT PRINTING
This method results in a raised design. A special chemical that burns or eats away at the fabric is used to lay the design. This method is often seen in velvet prints.
DISCHARGE PRINTING
Once the fabric is dyed, the design is printed with a paste that removes the color in that area, resulting in a "bleached" design. Colored pigment can also be added to the paste, which replaces the original color with a different color.
PHOTOGRAPHIC PRINTING
Photo-engraved rollers are used to print the image onto the fabric. This method is also used to create silk screens for screen printing.
|
There are many different ways to print on fabric, some of which have been around for millennia. Each method produces its own unique result, so all that remains is to select the process that offers exactly the required outcome. While some of these methods are only readily available for at-home projects, others can be carried out by knowledgeable technicians in a commercial setting.
|
To place an order:
upload your images online, and select "Fabric Dye-Sub Prints" product.
|
|
|
USA Giclee On Canvas, Fine Art Printing - Art Scanning & Reproductions - Handmade Oil Paintings - Custom Wood Panels, Metal Picture Framing - Block/Plaque Mountings, Large Format Dry Mounting & Lamination - Art Supplies: Stretcher Bars, Cradled Wood Panels and Artist Canvas - Collages On Canvas - Plexi/Acrylic Face Mounts - Block Acrylics, Fabric Printing, Dye Sublimation - Cityscape Skyline Prints, Resin, Photo Gifts and more...
|
|
© 2002-2025 - KeenART Media Ltd.
|
|
|
|